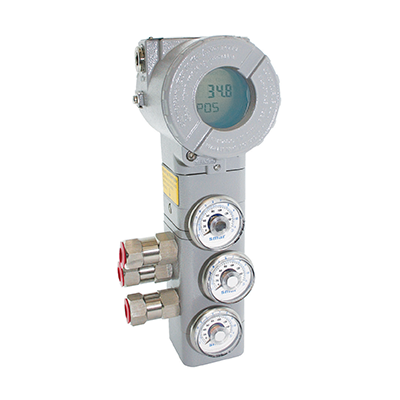
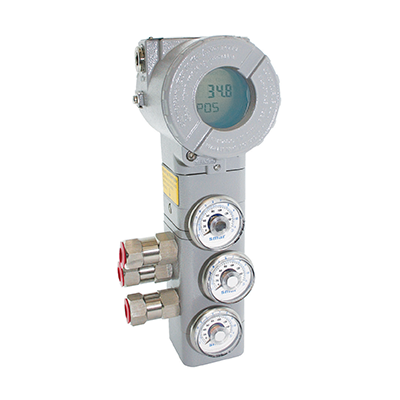
SMAR FY300 Series
Intelligent Valve PositionerThe FY300 digital positioner uses the most advanced microprocessor to perform accurate and fast valve positioning. The positioner is a controller that receives the setpoint from the main process controller and acts on the valve, moving it exactly to the ideal position, providing better process performance.
The FY300’s magnetic position sensor detects the actual valve stem position and takes corrective action according to the user’s configuration and control strategy. Non-contact position sensor (Hall Effect-based) reduces deficiencies in mechanical connections and levers.
The controller signal is processed on the main digital circuit board. Then an analog board receives the information from the main board and generates a low power voltage. This voltage is applied to a disk of piezoelectric material, resulting in a bending of this disk. This bending moves the disk away from or closer to the pressure transducer nozzle, which, as a consequence, results in a pressure variation (pilot), proportional to the signal from the controller of the control loop.
The block below the “Pressure Transducer” block contains a set of two diaphragms. These two diaphragms amplify the force related to pilot pressure and move the spool valve, releasing supply pressure on one side of the valve actuator. At the same time, the spool valve relieves pressure on the other side of the valve actuator to atmosphere.
The control valve stem will move in response to movement of the positioner spool valve. The actual valve stem position information is read by the magnetic position sensor (Hall Effect) and fed back to the main circuit board. With the position information, the microprocessor will send a command to the analog circuit, correcting the valve position whenever necessary.
The microprocessor uses the control algorithm to nullify the valve position error. Control parameters can be tuned using the magnetic tool or the portable configurator. It is also possible to configure the FY300 with applications based on FDT/DTM technology.
Types of Positioners
Linear
Configuration (local or remote) via software for strokes from 3 mm to 100 mm, with selection of linear magnet stroke options and mounting brackets.
Rotary
Configuration (local or remote) via software, rotation from 30° to 120°, used with suitable rotating magnet and mounting bracket.
Non-contact local Position Sensor
Standard positioner with integrated magnetic position sensor.
Remote, non-contact Position Sensor
More indicated in applications involving high temperature and vibration. It is also suitable for hard-to-reach places. Available in cable lengths from 5 m to 20 m.
Pressure Sensors
In addition to the usual information about valve and positioner status, pressure sensors provide important data that, further processed, allow advanced diagnostic activities of the control valve.
Double and single action
With the same positioner, it is possible to control the position of double-acting or spring-return valves.
Diagnostics and Parameterization:
FY301 (HART® Protocol) can be configured by:
- HI331 BLUETOOTH for android devices (App DEVCODROID) and Windows PC;
- Third-party configuration tools based on DD (Device Description) or DTM (Device Type Manager).
FY301, AssetView ensures continuous information monitoring.
The FY302 uses the H1 communication protocol, an open technology that allows any H1-enabled configuration tool to configure this equipment. SMAR’s Syscon (System Configurator Tool) is software used to configure, operate and maintain field equipment. Syscon provides efficient and user-friendly interaction using Windows NT version 4.0 or later, Windows 2000 and Windows XP.
Configuration tools such as AMSTM, FieldCareTM and HHT375 can configure FY302 equipment. DD (Device Description) and CF (Capability File) files can be downloaded from the SMAR page on the Internat of the Fieldbus FoundationTM.
The FY302 supports complex configuration strategies due to the high capacity and variety of instantiable function blocks. Fourteen types of function blocks are available and up to twenty function blocks can operate simultaneously. Fieldbus technology allows AssetView to access status and diagnostic information from the FY302. In this way, maintenance procedures become more effective, providing greater safety and plant availability. These instruments can be configured locally with the magnetic tool, without the need to open its cover, or remotely through SMAR’s ProfibusView or Siemens’ Simatic PDM.
PROFIBUS PA also provides quality and diagnostic information, improving plant management and maintenance. The EDDL (Electronic Device Description Language) and DTM files are available on the SMAR website.
FY300 Series control valve positioners are available in 4 to 20 mA versions and for HART® protocol, FOUNDATION™ fieldbus and PROFIBUS PA systems. The FY300 Series positioner provides a pressure output to the control valve actuator, positioning it according to input received from the output of a controller. The digital technology used in the FY300 Series allows an easy interface between the field and the control room with its own characteristics of each communication mode, considerably reducing installation, operation and maintenance costs.
- Suitable for most valve models and brands;
- A wide range of dedicated brackets for perso models and sizes from different control valve manufacturers;
- Linear movement from 3 mm to 100 mm; (for longer strokes, see our ACP300 Series catalog and the BFY-CL);
- Rotating movement from 30º to 120º;
- Locally or remotely configurable via HART® 4 to 20 mA protocol, FOUNDATION™ fieldbus and PROFIBUS PA;
- Rotating Local Indicator, user-friendly multifunctional;
- Easy installation, quick commissioning and adjustment;
- Continuous on-line diagnostics to reduce fault correction time and lower valve maintenance costs;
- Protection against transients;
- Histogram, step response in combination with asset management applications;
- Trend and load factor graphs available for diagnostics;
- Configuration of the valve characteristic curve in the most usual ways;
- Customized valve characteristic curve up to 16 points;
- Configurable Local Indicator;
- Password configuration protection;
- Multidrop operating mode;
- Position sensor without mechanical contact by Hall Effect;
- Remote sensor mounting for applications that are difficult to access or involve high vibration or high temperature;
- Supply air pressure from 20 psi to 100 psi;
- Certified for use in hazardous areas complying with EC (European Community) directives;
- Electromagnetic compatibility according to IEC 61000-6-2:1999, IEC 61000-6-4:1997 and IEC 61326:2002.
FY301 – HART® – 4 a 20 mA
- Local adjustment with magnetic tool without the need to open the equipment;
- HI331 BLUETOOTH Configurator for android devices (App DEVCODROID) and Windows PC;
- Configuration interface with DEVCODROID application on desktop or laptop;
- Remote parameterization and auto-configuration;
- Connectivity with Applications in the FDT/DTM (Field Device Tool/Device Type Manager) standard;
- Asset Management applications such as SMAR’s AssetView (for other applications, consult us);
- Supports DTM;
- Multidrop operating mode.
FY302 – FOUNDATIONTM Fieldbus
- Local configuration with magnetic tool, no need to open the equipment;
- 12 mA consumption current;
- Dynamic instantiation of blocks;
- Registered with Foundation Fieldbus™ and approved by ITK;
- 14 functional blocks.
FY303 – PROFIBUS PA
- Basic setup can be done using the magnetic tool, no need to open the equipment;
- Complete configuration is also performed with a remote configurator (eg ProfibusView from SMAR or Simatic PDM from Siemens);
- Function blocks for analog output and valve diagnostics;
- Current consumption of 12 mA;
- Supports DTM and EDDL.